When selecting rod ends for a new vehicle model, engineers consider several key factors to ensure optimal performance, durability, and safety:
Load and Application: The intended load and application dictate the type and size of rod ends needed. Factors such as the vehicle's weight, suspension design, and expected usage (off-road, racing, everyday driving) determine the load-bearing capacity required.
Material Selection: Choosing the right material for rod ends is crucial. Factors like strength, corrosion resistance, and weight play a role. Common materials include steel alloys, stainless steel, and sometimes specialized materials like titanium for high-performance applications.
Ball Joint Configuration: Rod ends come in various configurations, including male or female threads, straight or angled designs, and different attachment methods. Selecting the appropriate configuration based on the specific needs of the vehicle's suspension geometry and assembly is essential.
Environmental Conditions: Consideration of the vehicle's operating environment, including temperature variations, exposure to moisture, road debris, and potential corrosion factors, guides the choice of materials and protective coatings for rod ends.
Articulation and Misalignment: Rod ends should allow for proper articulation and misalignment to accommodate suspension movement without binding or restricting motion. This factor is critical for maintaining steering precision and overall suspension performance.
Sealing and Lubrication: Rod ends may have sealed or greaseable designs. Depending on the application, engineers evaluate whether sealed units or ones with grease fittings are more appropriate for maintaining optimal lubrication and extending component life.
Testing and Validation: Extensive testing under various conditions, including durability tests, load tests, vibration tests, and environmental tests, ensures that the selected rod ends meet performance and safety standards.
Cost and Manufacturing Considerations: Balancing performance requirements with manufacturing costs is crucial. Engineers strive to select rod ends that offer the necessary performance characteristics while considering cost-effectiveness in production.
Compliance with Standards: Rod ends must adhere to industry standards and regulations to ensure safety and compatibility with the vehicle's overall design and assembly.
By carefully evaluating these factors, engineers can select rod ends that are well-suited for the specific demands of the vehicle model, contributing to a reliable and efficient suspension system.
How do engineers address issues like corrosion or environmental factors affecting rod ends performance?Engineers employ various strategies to address issues related to corrosion and environmental factors affecting the performance of rod ends in vehicles:
Material Selection: Choosing materials with inherent corrosion resistance is fundamental. Stainless steel, certain alloys, and coatings like zinc plating or nickel plating provide a protective barrier against corrosion.
Sealing and Protective Coatings: Utilizing specialized seals, boots, or protective coatings on rod ends helps prevent moisture, dirt, and debris from infiltrating critical components. This protects the internal mechanisms from corrosion and wear.
Surface Treatments: Applying surface treatments like anodizing, chromate conversion coatings,
china rod ends manufacturer or powder coatings helps create a durable protective layer on the rod ends, enhancing their resistance to environmental factors.
Improved Lubrication: Using high-quality lubricants or incorporating self-lubricating materials into rod end designs can mitigate the effects of corrosion by reducing friction and minimizing metal-to-metal contact.
Design Enhancements: Redesigning rod ends to eliminate potential areas where debris or moisture can accumulate, such as improving drainage or modifying sealing mechanisms, helps prevent corrosion.
Corrosion Testing: Engineers conduct rigorous corrosion testing on rod end prototypes to simulate real-world conditions. This helps identify vulnerabilities and allows for adjustments to materials or designs to enhance corrosion resistance.
Environmental Testing: Subjecting rod ends to environmental tests involving extreme temperatures, humidity, salt spray, and other harsh conditions helps validate their resistance to corrosion and environmental factors.
Regular Maintenance: Recommending regular inspection and maintenance schedules for rod ends encourages timely detection of corrosion or wear. This includes cleaning, lubrication, and potential replacement of worn components.
Material Compatibility: Ensuring compatibility between different materials within the rod end assembly, such as matching metals and coatings, helps prevent galvanic corrosion caused by dissimilar materials.
By implementing these measures, engineers aim to enhance the durability and longevity of rod ends in vehicles, minimizing the impact of environmental factors like corrosion and extending the lifespan of suspension components.
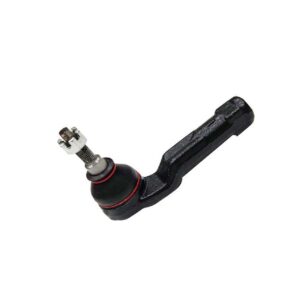